Additive manufacturing (AM) is a research focus at the University of Iowa Technology Institute. Scientists are studying how material-forming processes existing in nature can be used to enable next-generation AM technologies.
Research Topics
Next-generation AM technology development: We learn from nature to develop next-generation AM technologies that are multi-material, multiscale, ultra-fast, energy efficient, etc.
AM process modeling, quality control, and optimization: We use experimental and theoretical techniques to advance the understanding of the fundamental physics behind nature-inspired AM processes and achieve performance-driven process control.
Novel applications of new AM technologies: We use the unique capabilities of our AM technologies to create game-changing devices for various applications, such as tissue engineering, sensing, energy harvesting, and robotics.
During the past 30 years, the design and manufacturing community has benefited from AM, thanks to several of its advantages, including the capability to fabricate components with complex geometry. However, AM technologies also have critical issues such as poor surface finish, low resolution, insufficient material properties, and limited material selection. These disadvantages prevent wider application of AM in industries such as aerospace, defense, automobile, optics, electronics, biomedical, and energy.
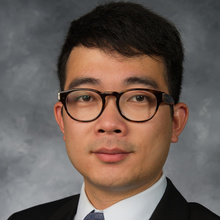
Since its establishment by Prof. Xuan Song in 2016, the The SONG Lab: Science Of Next-Gen manufacturing has invented and created several novel AM technologies to overcome the aforementioned problems. These include a multiscale and multi-material AM process, a support-free ceramic fabrication approach, a low-cost layerless direct metal drawing process, and an ultra-low-temperature ceramic fabrication technique. These new AM technologies have the capability to process a variety of materials, including polymers, ceramics, metals, and composites, into structures of arbitrary complexity, spanning multiple length scales, from several micrometers to several centimeters. More importantly, the cost and energy consumption in these new methods are dramatically reduced as well.
Project Examples
- Developed a novel prototype system to 3D print piezoelectric ceramic devices by integrating tape-casting and stereolithography techniques.
- Used 3D printing process to fabricate microstructures with high dielectric polymer/ceramic composite materials.
- Developed a multiscale stereolithography system, whose smallest feature could be as small as 5 µm, and whose building size could be as big as 50 mm.